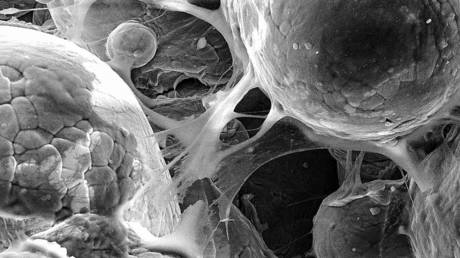
Biomedical researchers have begun creating porous structures from titanium alloys by smashing powder particles together at supersonic speeds in an extreme combination of 3D printing and spray painting.
The Cornell University-led team created the porous materials, that are allegedly 40 percent stronger than traditional manufacturing can achieve, using an existing 3D printing technique known as “cold spray.”
Normal additive manufacturing (3D printing) requires high temperatures to heat metals beyond their melting points so they can be shaped, but this can lead to issues including distortions in biomedical implants over time.
Instead, lead author Atieh Moridi and her team developed a method in which they used highly compressed gas to blast titanium alloy particles at a support structure, in a kind of ‘3D painting’.
“We focused on making cellular structures, which have lots of applications in thermal management, energy absorption and biomedicine,” said Moridi, assistant professor in the Sibley School of Mechanical and Aerospace Engineering.
The titanium alloy particles measure between 45 and 106 microns in diameter (a micron is one-millionth of a meter) and were fired at a substrate base, at 600 meters per second, faster than the speed of sound. The average bullet travels at 760 meters per second.
The titanium structures’ small size and porous texture make them an ideal candidate for use within the human body for implants such as joint replacements, according to the Cornell team.
The researchers had to find the goldilocks zone in order to make the materials stick, in between the alloy’s critical velocity, where it can form a dense solid and its erosion velocity, where it just disintegrates before a useful structure can form.
By locating the sweet spot just below the titanium alloy’s critical velocity, the team was able to create porous but sturdy structures ideal for creating artificial joints for the knee or hip, or for use in cranial and facial reconstruction implants after a traumatic injury.
Furthermore, patients’ bones are able to grow inside the structures allowing them to properly fix in place and maintain biomechanical integrity, while reducing the need for possible follow-up surgeries significantly.
“This helps reduce the likelihood of the implant loosening. And this is a big deal. There are lots of revision surgeries that patients have to go through to remove the implant just because it’s loose and it causes a lot of pain,” Moridi said, adding that the technique has larger-scale industrial applications including in the construction, transportation and energy sectors.
Think your friends would be interested? Share this story!